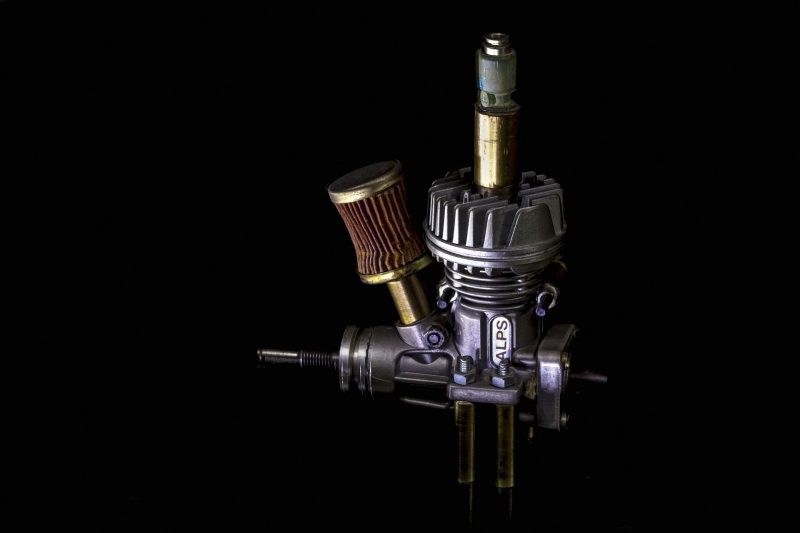
工場における機械の運用管理には、さまざまなセンサーが重要な役割を果たしている。特に、温度計は極めて基本的かつ必要不可欠なデバイスである。温度計は製造プロセスの適切な温度管理を行うために用いられ、温度の監視は製品の品質を保つために必要不可欠である。工場では、温度測定の精度が特に重視される。
温度が過度に上昇すれば、設備自体に悪影響が及ぶ可能性がある。また、冷却が不十分な場合には、製品に致命的な問題を引き起こすことも考えられる。このため、温度計によりリアルタイムで温度を監視し、異常があれば速やかに対応する仕組みが構築されている。これが、工場の安全性や生産効率、さらには製品品質の向上につながる。
温度計にはいくつかの種類があり、用途に応じて選択される。例えば、接触式の温度計は、測定対象に直接接触して温度を測るため高精度が求められる場面に適している。一方、非接触式の温度計は、物体から放射される赤外線を利用し、接触しないで温度を測定する。これにより、危険な場所や高温の部品に対する安全な測定が実現可能となる。
工場内では、多くの場合、温度計はPLC(プログラマブル・ロジック・コントローラ)と連携している。PLCとは、工場自動化に用いられるコンピュータの一種で、さまざまなセンサーからのデータを集約して処理する機能を持っている。温度計がセンサーとしてつながることで、工場全体の運用が効率化され、温度に基づく制御が常に行えるようになる。この制御は、自動的に冷却機器の稼働を調整したり、異常時に警告を発するなど、さまざまな形で具体化される。
温度計のセンサー技術は日々進化しており、より高精度かつ迅速な測定が可能になる傾向にある。例えば、デジタル温度計においては、温度データが瞬時にディスプレイに表示されるだけでなく、外部のデータ処理システムと連携して、分析が行える仕組みが整備されている。また、IoT技術の発展により、温度計から取得したデータをクラウドに送信し、遠隔地からでもリアルタイムに状況把握ができるようになるなど、利便性が飛躍的に向上している。温度管理の重要性は、製品がその機能や品質を維持するためには欠かせない。
このため、一貫した温度管理の仕組みと実施が求められる。ここで重要なのが、温度計の定期的なメンテナンスである。センサー自体が劣化したり、汚れが付着することで誤測定をすることがあるため、定期的な校正が不可欠である。適切な校正を行うことで、常に信頼性のあるデータを基にしたプロセス制御が実施可能になる。
温度計における技術革新も目を見張るものがある。最近では、ワイヤレス技術の導入が進み、配線の手間を省くことが可能となった。こうした進化により、工場内のあらゆる測定ポイントに設置することが容易になり、全体的なデータの網羅性が向上している。エネルギーコストの削減や生産効率の向上を実現するためには、温度計を始めとする各種センサーの正確な実装と運用が不可欠である。
温度計をはじめとするセンサーがもたらすデータは、工場オペレーションの可視化にも寄与する。温度の変化をモニタリングすることで、製造プロセスの改善点を見出す手がかりが得られる。また、このようなデータを元に製造メンバーが協働で問題解決に取り組むことで、さらなる効率化を図ることができる。このように、温度計は工場内での機械管理において極めて重要な役割を果たしている。
リアルタイムで温度を測定し、そのデータを基にした高速な意思決定が可能になることで、製品の品質が大きく向上する。さらに、センサー技術の進化により、温度管理のみならず、様々な制御される環境が整備される中で、工場の生産性が高まるとともに、将来的に持続可能な製造プロセスが実現されることが期待される。これからも温度計をはじめとした各種センサーの役割は、工場運営においてますます重要度を増していくことだろう。センサー技術のさらなる革新を通じて、より効率的で安全な生産環境を実現するための努力が続けられる必要がある。
温度測定の信頼性と精度を高め、リスクを最小限に抑える取り組みは、進化する技術とともに進展していくと考えられる。温度計は単なる測定器であるにとどまらず、安全で高度な工場運営の基盤を支える重要な存在である。工場における機械の運用管理で、温度計は重要な役割を果たす基本的かつ必要不可欠なデバイスである。製造プロセスにおいて適切な温度管理は製品品質を保つために欠かせず、温度測定の精度が特に重視される。
温度の過度な上昇や冷却不足は設備や製品に悪影響を及ぼす可能性があるため、リアルタイムでの温度監視体制が必要である。これにより、工場の安全性、効率、生産性が向上する。温度計には接触式と非接触式の2種類があり、用途に応じた選択が求められる。接触式は高精度な測定が可能であり、非接触式は危険な環境や高温の部品への安全な測定が実現できる。
多くの工場では、温度計がPLC(プログラマブル・ロジック・コントローラ)と連携し、データを集約することで運用効率が向上する。PLCによる温度ベースの制御は、自動的な冷却機器の稼働調整や異常時の警告を可能にする。さらに、温度計の技術も進化しており、デジタル温度計の導入によりデータのリアルタイム分析が可能となった。IoT技術の発展により、温度データはクラウドに送信され、遠隔での状況把握が容易になるなど利便性が向上している。
製品の機能や品質の維持には一貫した温度管理が必要であり、定期的なメンテナンスや校正が不可欠である。これにより、常に信頼性の高いデータに基づくプロセス制御が可能となる。また、ワイヤレス技術の導入により、配線の手間が省かれ、工場内の測定ポイントに容易に温度計を設置できるようになった。このような技術革新がエネルギーコスト削減や生産効率向上に寄与する。
温度計をはじめとするセンサーがもたらすデータは工場オペレーションの可視化を実現し、製造プロセスの改善に役立つ。製造メンバーがデータを元に協力して問題解決に取り組むことで、さらなる効率化が図れる。このように、温度計は工場内の機械管理で極めて重要な役割を果たし、リアルタイムの温度測定に基づく迅速な意思決定を可能にする。センサー技術の進化により温度管理に加え、様々な制御環境が整備され、工場の生産性が向上するとともに、持続可能な製造プロセスの実現が期待される。
今後も温度計や各種センサーの役割はますます重要性を増すと考えられ、効率的で安全な生産環境の実現に向けた努力が必要である。
No comment yet, add your voice below!